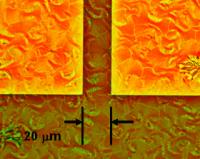
|
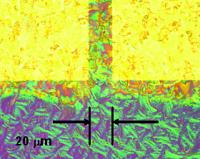
|
Optical micrographs of typical
FET structures in the NIST/Penn State/UK experiments show the
effect of pretreating contacts to promote organic crystal
formation. Treated structure (l) shows crystal structure extending
from the rectangular contacts and merging in the channel in
contrast to untreated contacts (r).
Images � by NIST |
A simple surface treatment technique
demonstrated by a collaboration between researchers at the National
Institute of Standards and Technology (NIST), Penn State and the
University of Kentucky potentially offers a low-cost way to mass
produce large arrays of organic electronic transistors on polymer
sheets for a wide range of applications including flexible displays,
�intelligent paper� and flexible sheets of biosensor arrays for field
diagnostics.
In a paper posted this week, the team describes how a chemical
pretreatment of electrical contacts can induce self-assembly of
molecular crystals to both improve the performance of organic
semiconductor devices and provide electrical isolation between devices.
Organic electronic devices are inching towards the market. Compounds
with tongue-twisting names like �5,11-bis(triethylsilylethynyl)
anthradithiophene� can be designed with many of the electrical
properties of more conventional semiconductors. But unlike traditional
semiconductors that require high-temperature processing steps, organic
semiconductor devices can be manufactured at room temperature. They
could be built on flexible polymers instead of rigid silicon wafers.
Magazine-size displays that could be rolled up or folded to pocket
size and plastic sheets that incorporate large arrays of detectors for
medical monitoring or diagnostics in the field are just a couple of
the tantalizing possibilities.
One unsolved problem is how to manufacture them efficiently and at low
cost. Large areas can be coated rapidly with a thin film of the
organic compound in solution, which dries to a semiconductor layer.
But for big arrays like displays, that layer must be patterned into
electrically isolated devices. Doing that requires one or more
additional steps that are costly, time-consuming and/or difficult to
do accurately.
The NIST team and their partners studied the organic version of a
workhorse device - the field effect transistor
(FET) - that commonly is used as a switch to,
for example, turn pixels on and off in computer displays. The
essential structure consists of two electrical contacts with a channel
of semiconductor between them. The researchers found that by applying
a specially tailored pretreatment compound to the contacts before
applying the organic semiconductor solution, they could induce the
molecules in solution to self-assemble into well-ordered crystals at
the contact sites. These structures grow outwards to join across the
FET channel in a way that provides good electrical properties at the
FET site, but further away from the treated contacts the molecules dry
in a more random, helter-skelter arrangement that has dramatically
poorer properties - effectively providing the
needed electrical isolation for each device without any additional
processing steps. The work is an example of the merging of device
structure and function that may enable low cost manufacturing, and an
area where organic materials have important advantages.
In addition to its potential as a commercially important manufacturing
process, the authors note, this chemically engineered self-ordering of
organic semiconductor molecules can be used to create test structures
for fundamental studies of charge transport and other important
properties of a range of organic electronic systems.
|